Photoelectric sensors are one of the standards in today’s factory automation. As machine designs become more compact, sensors must be placed in places that are difficult to reach. For applications in which conventional photoelectric sensors have reached their limits in terms of size and power, the Micromote system has been developed. Working without optical fibers, it is small, powerful and innovative.
Increasing demands on photo electric sensors: handling miniaturization
The further development of sensors today is regarded as a pacesetter in industrial automation. In general, sensors reflect our human senses on a machine. To do this, they perceive the physical or chemical states of a machine and then convert these into electrical signals. This enables us to monitor and control the process workflow and, further, to improve it. Special advantages of the applications include inductive sensors for the detection of mechanical components within a machine and photoelectric sensors for detecting a wide variety of objects. The technical requirements for sensors in general, and, photoelectric sensors in particular, have risen accordingly in recent years.
Derived from the requirements of parts manufacturers and machine builders, the topic of miniaturization is still an important requirement from the point of view of a manufacturer of automation components. In addition, an ever-increasing degree of automation of the machine is a need to be solved.
With the help of modern manufacturing technologies for sensors one can meet these requirements. For example, photoelectric sensors have been available on the market for some time and have continued to evolve in this way and also in technical terms. Especially important, the optical components are no longer qualitatively unstable. LEDs are smaller and more powerful than when they were first introduced. Thanks to the possibilities offered by microelectronics, there are already many sensors with impressive technical data on the market today.
Use of fiber optics
In order to offer more possibilities to build compact machines and, nevertheless, to integrate sensors, fiber optics have been introduced. Fiber optic cables can transmit light almost lossless over longer distances. Therefore, the distance to the application, the place where the light is actually needed, can be larger. The light is generated and resumed in an external evaluation unit located in the control cabinet or further away. In automatic machines nowadays, glass fibers are used in very large and steadily growing quantities. The technology has proven itself and is often used as a standard solution.
Nevertheless, optical fibers have disadvantages that often only require unsatisfactory compromises among machine manufacturers. One disadvantage is already apparent in the integration. Due to the stiffness of the fibers, radii must be chosen larger to prevent cracks in the fiber resulting in power loss. It is not uncommon for long-term alternating loads (bending and torsion loads) to lead to failure of the sensor.
Furthermore, considerable disadvantages arise in applications with regular maintenance or adjustment work on the integrated plant components, e.g. during a format change. Here, the rigidly installed fiber must be at least partially dismantled, which costs time and money accordingly.
Customer-specific solutions on housings cannot be realized so easily. But that is mainly because fibers optics are produced in mass production. In addition to the typical sensor functions, increasingly complex requirements are addressed to the mechanical engineering to produce high-tech products. This repeatedly leads to customized sensor solutions being used. A sensor manufacturer must therefore set up its portfolio accordingly flexible. Even if it seems surprising that a special solution should be the better and also cheaper solution, especially in an area where complex applications are solved, this is reflected in a clearly thought out modular approach of a system consisting of standard components.
Another risk factor is optical performance. The reduction of the opening angle of the light beam is necessary to achieve the long ranges and high resolutions. In the case of fiber optics, this is only possible by using additional lenses, which, due to their mechanical dimensions, negate the space advantage, at least in part.
Electricity instead of light
A technical alternative is a system that transmits power instead of light. The Micromote series (The name “MICROmote” consists of “Microsensor” and “Remote Amplifier”) provides the user with a particularly high optical performance in a small space, which is due to special miniaturized LED, photodiodes and phototransistors. Due to the modular principle, the user can quickly find the right solution for almost any application.
Both systems — fiber optic-based systems and Micromote series — are similar in their basic structure. Both systems have one or two sensor heads and a separate evaluation unit (amplifier). However, in the Micromote series, no light is transmitted to the application to get state information from the “scene of the event,” but it instead uses electricity. The light is generated exactly where it is needed. Therefore, depending on the application, the sensor heads (transmitter and receiver) are connected to an amplifier via a flexible electrical cable sheathed with various materials. The cables used offer a very high flexibility (1.6 mm bending radius) and can therefore be laid effortlessly, in accordance with the spatial requirements of the machine – whether around corners or edges. In addition, the cable has outstanding properties in terms of tear and breaking strength (treated Kevlar strands, PUR jacket). The cable used, which is, for the most par,t mechanically fatigue-free, provides a reliable means of transmitting the electrical base signal, even in drag chains (4,000,000 cycles, tensile strength up to 90 kg). This also makes it possible to integrate sensor cables in wiring harnesses or, for that reason, is also optimally suited for sensor applications in or on moving machine parts (for example in robot grippers and on slides).
Electrical couplings for fast cable separation without sensor removal
Let’s take another look at the two fiber optic systems. Micromote is more accurate. When changing format, quick disconnection of cables at a convenient location (such as a power outlet) is the ideal solution. Such sockets are not available for fiber optics, at least in an economically acceptable form. By such electrical couplings, the sensors can be installed and left unchanged. The electrical leads to the measuring point are only separated at the plug connection, allowing the work on the removed components to be done easily and thus quickly. Then the module is installed, and the sensor cables reconnected. It may not even be necessary to re-adjust the sensor system. In addition, the Micromote system concept uses standardized M8 connectors, both for the supply and the sensor head.
However, the advantages of this alternative to fiber optics are not limited to the use of electrical signal transmission from sensor head to external evaluation unit. The used LED or phototransistor elements of Micromote sensors with integrated high-performance optics in various sizes, which are installed in the sensor heads, allow for comparable dimensions of the sensor elements and larger lens distances usually at a much higher resolution, resulting in a significant performance improvement. For another, they have none of the typical drawbacks associated with fiber optic systems. On the contrary, they can offer decisive advantages, such as the simple implementation of customer-specific requirements (e.g.: shape, material, length) – these can be implemented quickly and inexpensively. This approach is often the better choice for the OEM as well as for the end user in every respect.
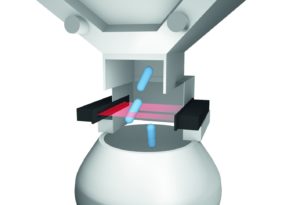
Conclusion
Miniaturization remains the general trend in almost all areas of electrical automation. Fiber optics was a pioneering application in the field of photoelectric sensors. Many areas of industrial automation are now unthinkable without fiber optics, although they have considerable disadvantages in some areas. However, due to its specific advantages, fiber optics will continue to be the preferred technical solution in many areas, for example, in situations of increased individual temperatures (typical application for fiber optics) or in very strong electromagnetic fields (e.g., welding fields).
The fundamental cost-driven trend towards standardization of sensors in machine and plant engineering meets growing demands on optical performance as well as the desire for customization, specific sensor solutions that take into account the specific conditions of the company and can be implemented in the appropriate application, i.e. wherever extreme flexibility is required, be it sensor cables or the used materials or the optical components. So there, the Micromote-system approach is a better alternative to fiber optics.
[youtube https://www.youtube.com/watch?v=ZIpbWxs2_iM]
Find out more about the possibilities and the product portfolio of the Micromote series at balluff.com
[…] A safety version of a position feedback sensor increases the security of operations. Additionally LED based photoelectric sensors detect even smallest amounts of liquids or […]
This Blog is very useful and informative.
<a href=”https://alignexperts.com/food-consultants/”>food packaging consultant</a>