Nach „Kranplätze müssen verdichtet sein“ folgt: Die Kranposition muss gemessen werden. Doch warum sollte die Position eines Brücken- oder Deckenkrans, wie auch oft in großen Lagerhallen zu finden, gemessen werden? Dessen Position sollte doch offensichtlich zu erkennen sein, oder?! Aber: Wenn es in Zeiten von Digitalisierung und Industrial Internet of Things um Automatisierung geht, ist die exakte Positionsmessung von Kränen entscheidend. Denn nur durch das Wissen über die genaue Position lassen sich nicht wertschöpfende Prozessschritte, wie zum Beispiel der Materialtransport zur, während oder aus der Produktion sicher automatisieren.
Hieraus ergibt sich die nächste Fragestellung: Wie soll oder kann die Positionsbestimmung eines Krans funktionieren?
Für die Wegmessung eignen sich verschiedene Technologien und Systeme. Jede Lösung hat dabei individuelle Vor- und Nachteile. Optische Laser-Systeme beispielsweise sind anfällig für Verschmutzung; magnetostriktive System hingegen nicht. Um das nochmal festzuhalten – in diesem Beitrag geht es übrigens um letztere. Magnetbasierte Wegmesssysteme bieten außerdem den Vorteil nahezu wartungsfrei zu sein, da das System ein verschleißfreies und vor allem berührungsloses Funktionsprinzip nutzt. Bei optischen Systemen ist dies nicht der Fall. Hier können Vibrationen dafür sorgen, dass Lichtquellen neu ausgerichtet und Systeme in der Zwischenzeit stillgelegt werden müssen. Einen hilfreichen Artikel zur Funktionsweise gibt es auch hier zu lesen.
Unabhängig davon benötigt ein magnetostriktives System, wie der Name bereits vermuten lässt, zusätzlich zum Längenmesssystem zu positionierende Magnete. Diese können beispielweise entlang der Verfahrschiene eines Krans befestigt werden, um die Position genau zu bestimmen. Sind diese positioniert, ist das System auch schon fast fertig installiert. Ein zusätzlicher Vorteil: Die Magnete können flexibel positioniert werden, so dass bestehende Schienen oder Geländer genutzt werden können. Damit ist eine Integration in bestehende Systeme einfach umzusetzen.
Eine beispielhafte Applikation in der Intralogistik kann wie folgt aussehen:
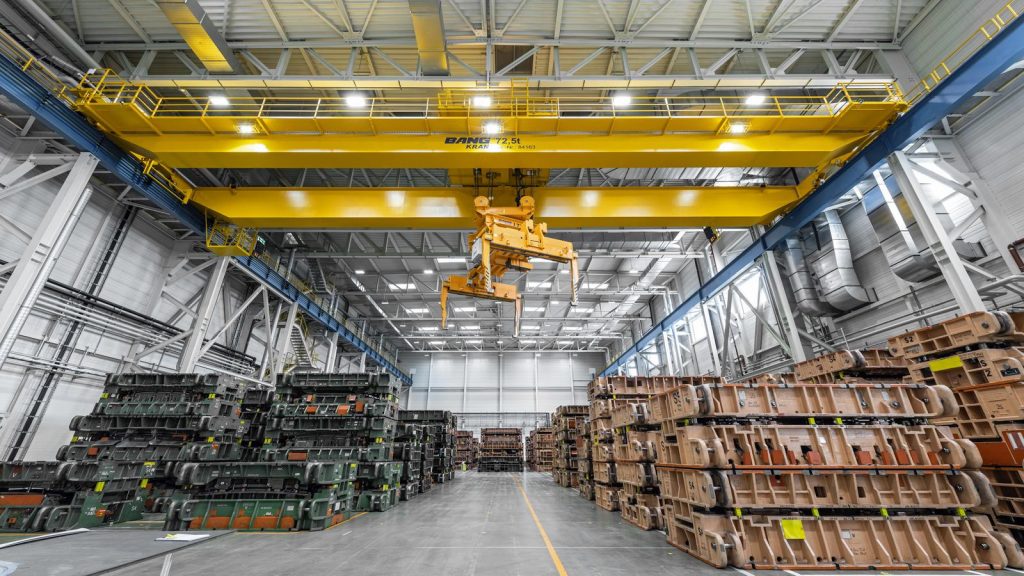
In verschiedenen Industrien werden Brückenkräne eingesetzt, um beispielsweise schwere Metalplatten zu bewegen. Das stellt einen klassischen Anwendungsfall für das LDPS (Long Distance Positioning System) dar, welches zur genauen Positionsbestimmung eingesetzt werden kann. Dabei wird das Messsystem am Kran, in Nähe der Schiene mit den befestigten Magneten, angebracht. Wird der Kran nun auf dieser Schiene bewegt, erfasst das Messsystem die Position der Magnete, an denen es vorbeifährt. Durch die unterschiedlichen Abstände zwischen allen Magneten, kann das System die Position des Krans exakt ermitteln. Einzige Voraussetzung: Es müssen sich jeweils mindestens zwei Magnete im Messbereich des Messsystems befinden.
Ist das System installiert, ermöglicht es die automatisierte Steuerung des Krans und erhöht gleichzeitig die Sicherheit, denn Unfälle aufgrund von manueller Steuerung können ausgeschlossen werden. Dabei sind selbst große Distanzen kein Problem. Das LDPS macht seinem Namen alle Ehre, denn es kann Distanzen von vielen hundert Metern problemlos abdecken, ohne Minderung der Genauigkeit in der Positionsbestimmung (Wiederholgenauigkeit 0,5 mm).
Das LDPS stellt dank zuverlässiger und flexibler Positionsmessung über mehrere hundert Metern selbst in rauen Umgebungsbedingungen ein perfektes Messsystem für große Distanzen dar. Daher ist es für Anwendungen an Laufkränen, Verladebrücken, Portalkränen, Umfahrsteuerungen sowie für die Kran-und Katzfahrt bestens geeignet und macht Prozesskräne zu Großraumrobotern.
Beim klicken auf das folgende Applikationsbild gelangen Sie zu einem Govie in dem die Funktion des LDPS simuliert wird:
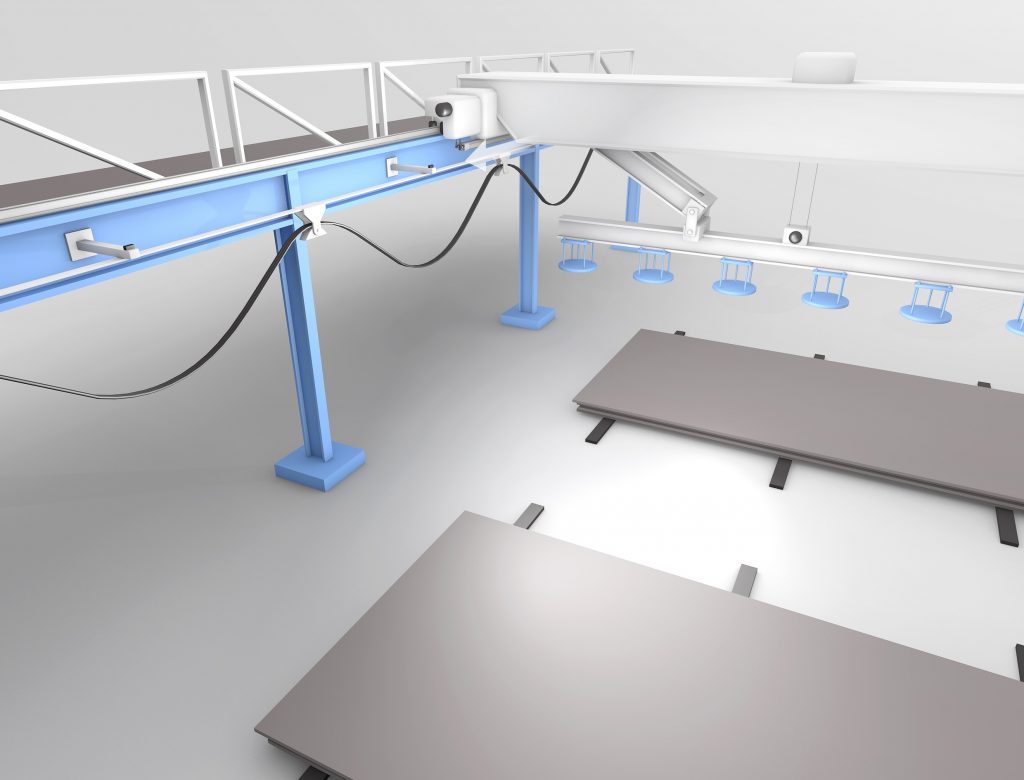
Link zur Produktübersicht LDPS
Danke für den interessanten Artikel! Gerne würde ich auch noch mehr über die Vor- und Nachteile anderer Technologien und Systeme für die Wegmessung lesen. Auch bin ich erstaunt, dass das LDPS so flexibel in seiner Anwendung ist.
Viele Grüße
Antonia